Manufacturing Shift Scheduling: Best Practices, Schedule Types, And Software Solutions
Try When I Work for free
Without people, there’s no manufacturing.
That’s why paying attention to how you schedule your employees should top your list of concerns.
Manufacturing shift scheduling is tricky and has traditionally been a manual process of spreadsheets and phone calls with shift schedules posted in break rooms or locker rooms. That no longer works in today’s technological age where people live on their phones and expect to access information relevant to them whenever they want.
Understanding manufacturing shift schedules is the first step towards revamping your process to one that works, both for your employees and for you.
In this comprehensive guide to manufacturing shift scheduling, you’ll discover the importance of effectively scheduling your employees to meet production demands. We’ll walk you through various scheduling approaches, best practices, and how to improve your overall manufacturing management process using modern scheduling tools.
“When I Work creates streamlined communication for the entire team.”
– Bob Burns, Project Manager, Goyette Mechanical
Key takeaways
- Manufacturing shift scheduling involves assigning work times to employees to ensure complete coverage that meets production demands.
- Effective employee scheduling is not just about filling in spots; it’s about empowering employees, respecting their work-life balance, and using real-time data for forecasting future needs.
- Common shift schedules in manufacturing include fixed shift schedules, split shift schedules, overtime shift schedules, rotating shift schedules, on-call shifts, and no-schedule shifts.
- Effective shift scheduling can lead to reduced labor costs, increased productivity, better work culture, and improved employee retention.
- Using modern scheduling software like When I Work can greatly simplify the complex task of managing manufacturing schedules.
Table of contents
- What is manufacturing shift scheduling?
- How to craft effective manufacturing schedules
- Manufacturing shift scheduling best practices
- Common types of shift work schedules
- How do labor laws impact shift scheduling in manufacturing?
- How to pick the right schedule for your team
- Benefits of effective manufacturing schedules
- Using When I Work to schedule manufacturing employees
- Manufacturing shift schedules FAQs
Looking to learn about rotating shift schedules? Keep reading or watch our YouTube video and learn about the various types of rotating shift schedules, determine which is right for you, and how to create a more balanced schedule that benefits your employees and your business.
What is manufacturing shift scheduling?
Manufacturing shift scheduling is simply assigning work times to your employees for complete coverage that meets production demands.
To do that, you’ll:
- Define work shift lengths
- Choose shift schedule types
- Determine overtime policies
- Determine scheduling policies
It seems simple, but can become pretty complicated once you move from theoretical to actually scheduling people to meet manufacturing demands.
How to craft effective manufacturing schedules
Improving your manufacturing management process includes understanding how to properly schedule employees. You’re not just writing names on a calendar to fill in blank spots.
Effective employee scheduling is about empowering employees and respecting their work-life balance. To make that happen, you should know what your team needs to accomplish, an understanding of how busy (or slow) production is during different times of the day, and data that allows for forecasting changes in the future.
In other words, it means you need to:
- Understand your schedule. You can’t optimize your manufacturing shift schedule if you don’t understand it. For that, you need data that allows you to see what’s happening in real time, what’s happened historically, and what might happen in the future (labor forecasting).
- Practice dealing with the unexpected. It’s easy enough to throw overtime at every labor problem that suddenly crops up, but that’s expensive. Taking a scheduling approach that doesn’t involve overtime as the go-to solution is more difficult, but makes a difference in the long-run.
- Stay in communication. Talk to your managers and employees to find out what is and isn’t working with the schedule. Effective scheduling that looks good on paper but fails in the real world is simply that: a failure.
When I Work makes all of this easy. You’ll be able to use in-depth reporting of your schedule and time tracking to know what’s going on with your labor costs. You can use alerts and notifications to manage overtime and employee availability. You’ll also be able to keep the lines of communication open with team messaging, right within the platform. Everything you need to know about your manufacturing schedule is at your fingertips.
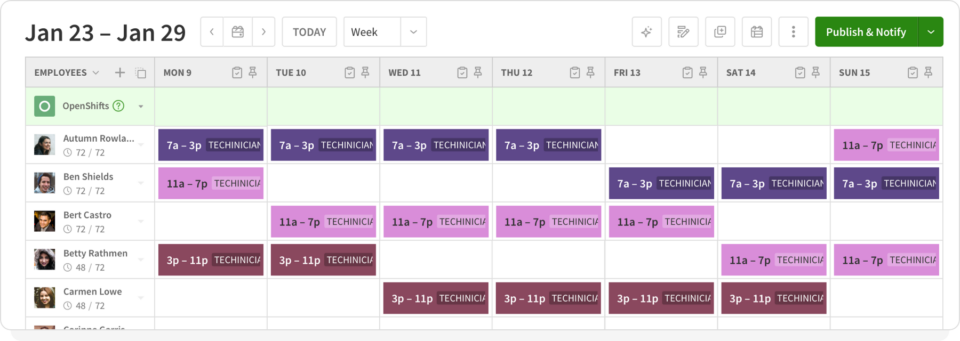
Common manufacturing shift scheduling challenges
Scheduling manufacturing shifts comes with its fair share of challenges. Here are some common issues and how you can address them:
- Dealing with unexpected absences: When one person can’t make it in for their shift, it messes up the entire production line. You have to scramble to find a replacement quickly or you run the risk of lost productivity. When you use scheduling software, you can quickly post the shift for someone to pick up, so you don’t have to spend all your time texting and calling employees.
- Managing overtime: It’s easy to just schedule as many people as you need and not pay attention to how much you’re spending in overtime, but controlling labor costs is essential to your bottom line. Use scheduling software that gives you notifications when you schedule employees for overtime, and alerts you when a worker is about to go into overtime hours to manage your labor costs.
- Preventing burnout: Tired employees make mistakes. When you’re scheduling long hours or rotating shifts, you have to ensure your workers are getting enough rest. Scheduling software with automatic rules around rest periods and time between shifts can help you make sure your employees are getting enough downtime to be happy and productive.
Manufacturing shift scheduling best practices
When you understand how to schedule employees effectively, you can put into place several best practices:
- Plan ahead: Last-minute scheduling, or constant rushed changes, are frustrating to employees. They may have made plans, or are already overworked. Schedule in advance, and build and publish upcoming schedules at regular times so employees know when to expect the schedule to come out.
- Plan far ahead: Be ready with a plan for sudden schedule changes, and communicate that with employees so they aren’t surprised.
- Comply: Federal and local laws, as well as any internal HR or union agreements, have to be followed when building your schedule.
- Communicate: Let your employees know the upcoming schedule as soon as it’s ready, and communicate any contingency plans that might affect them.
- Make it accessible: It shouldn’t take heroic effort to see the schedule, so make the schedule as accessible as you can for all employees.
Common types of shift work schedules
When it comes to choosing which manufacturing shift schedule to use, you have options. Each has its own benefits (and challenges); most can be mixed with other types on the same calendar. Since manufacturing is often 24/7, you’ll need to build a 24-hour shift schedule.
Fixed shift schedules
A fixed shift schedule is one of the most common approaches, and also one of the easiest to manage when it comes to planning and being compliant with federal labor laws.
With fixed shifts, employees have regular shifts in which they work the same days, and hours each day, every week.
Fixed shift schedules provide stability and allow employees to balance work and personal life easier because their schedule is predictable.
This schedule may not be the best for manufacturing businesses if you need to run your plant for more than eight hours a day. Workers on the second and third shifts may want a chance to work during their day for their work-life balance, and a fixed schedule doesn’t give them the opportunity for flexibility.
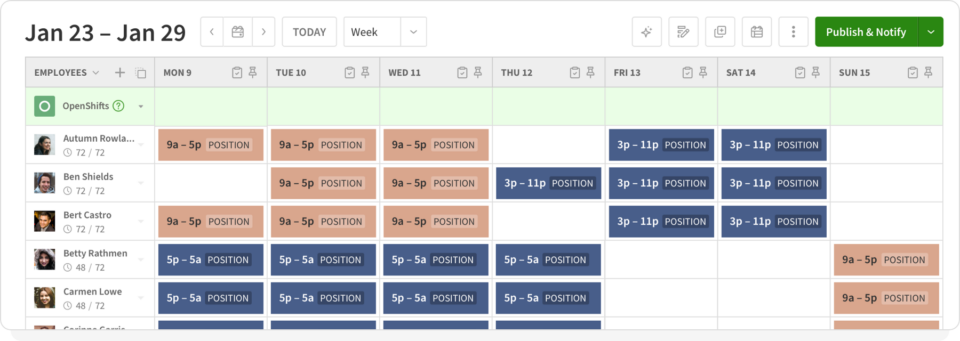
Split shift schedules
Split shifts are exactly what they sound like: regular shifts split into parts. Instead of an employee work day that is a single block of time, the day is divided into two or more parts. Typically, a shift is split by at least two hours.
Split shifts are helpful for employees who have obligations that fall during a traditional shift, such as picking up a child after school.
This schedule isn’t the best for manufacturing plants, as it can cause line disruptions throughout the day.
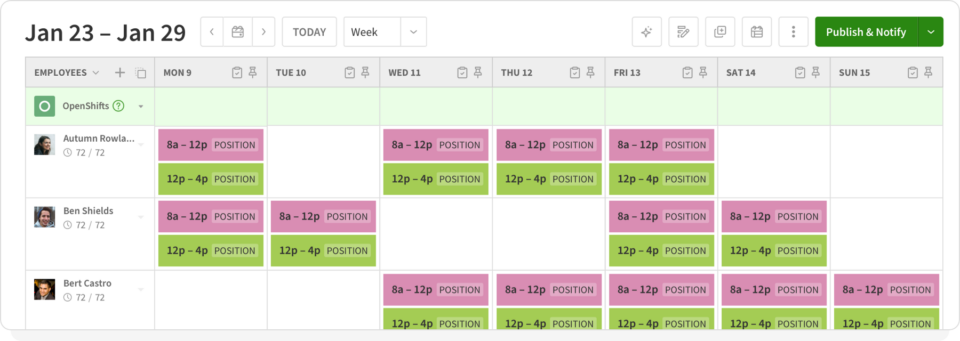
Overtime shift schedules
Overtime shifts are when employees work longer than a typical shift. Overtime shifts come with extra pay, and that means your labor costs can get out of control if you rely on them too much. They can also lead to employee burnout.
Managing overtime in manufacturing is especially tricky; it’s useful during temporary situations where labor is short or demand is high, but it’s easy for a temporary fix to become standard practice.
Some employees like overtime because of the extra pay, but they might unwittingly burn themselves out if you don’t stop them. Required overtime, due to persistent labor shortages, can have a negative impact on turnover.
Rotating shift schedules
Rotating shifts are a set cycle of shifts that your employees switch through over a set period of time. Not all shifts are equally preferred by employees, so rotating shifts make things fair by having all employees eventually work all shifts at some point.
Not all rotating shifts are set up the same way. You might have something as basic as day shift and night shift. For businesses like manufacturing, which are often running 24/7, you might have day shift, swing shift, and night shift.
Rotating shifts can also have different frequencies when it comes to the rotation. Frequent rotation can be hard on employees’ physical and mental health, while slower rotation gives them time to adapt and adjust.
Rotating shifts are great for manufacturing plants that run constantly. This shift schedule gives employees the ability to work days and nights, making the division of shifts fair and predictable, so they can plan their lives around work.
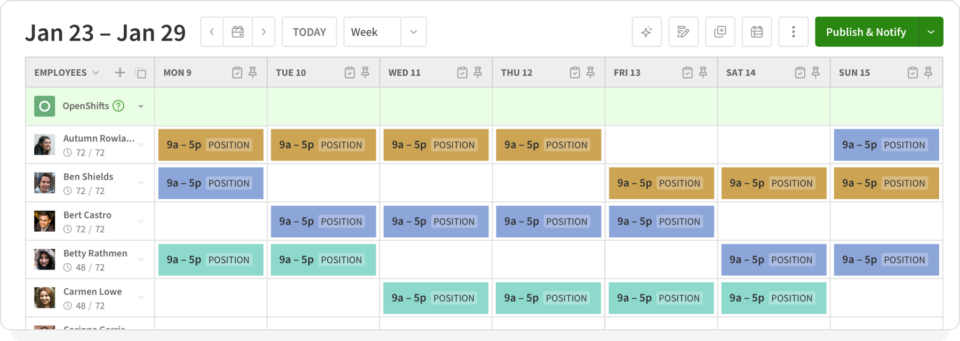
On-call shifts
On-call shifts means that an employee is available to work on demand, should the need arise. Employees who are on call may be used to fill in for absent employees or during emergencies when more help is needed.
On-call shifts can be a burden on some employees, as they aren’t at work but can’t make plans. For this reason, they are often compensated more, and are rotated through the staff so everyone has their turn.
These types of shifts can be great for plant flexibility, in case of business needs or absenteeism, but they can cause confusion and chaos if your on-call workers aren’t specifically trained for the positions you might need them to fill. And making sure you have on-call availability for every possible position probably isn’t feasible, so this may not be the best way to schedule your manufacturing shifts.
No-schedule shifts
Don’t let the name fool you!
No-schedule shifts are still scheduled, just like any other shift. The difference is that they aren’t as regular as the other shifts we’ve covered. Scheduling managers put employees on the schedule wherever they’re needed, and it might differ from week to week based on need.
These shifts can be difficult for employees as they prevent a good work-life balance. Employees never know what their schedule will be from one week to the next. No-schedule basically means unpredictable, from the employee’s point of view.
The lack of predictability in these shifts probably isn’t right for manufacturing plants. You need to be sure you have the right workers, with the right qualifications, available at all times. That means precise scheduling or you risk line interruptions and/or mistakes.
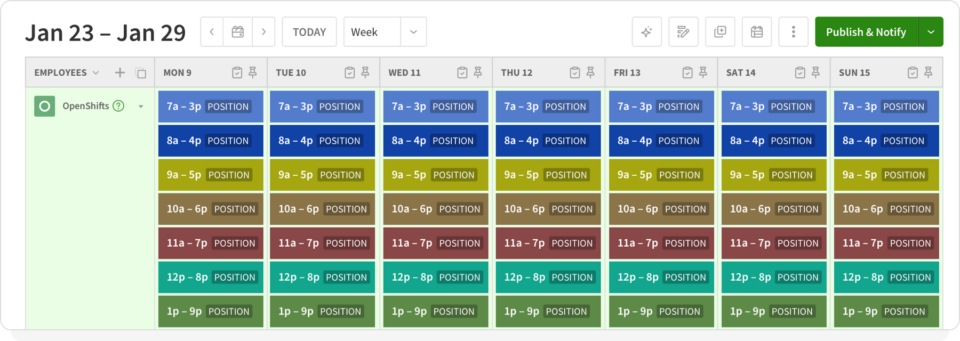
When I Work can make it easy to schedule these different types of shifts. You can name them accordingly or even color-code them so your team knows exactly what kind of shift they have.
How do labor laws impact shift scheduling in manufacturing?
Labor laws, especially predictive scheduling laws, can have big impacts on your plant’s scheduling processes. Last-minute changes could cost you fines and reputational damage. Be sure you’re in compliance with your local and state laws, as they can differ from city to city and state to state. Your best bet is to make sure you release your schedule early, with good labor forecasting so you can minimize overtime costs.
How to pick the right schedule for your team
Choosing the right schedule for your manufacturing team will take into account a lot of factors. What are your production goals? How many people do you have working at any given time? What skill sets do you need on any given shift? Make sure you consider your business goals along with the needs of your employees. Ask the team for feedback, too. They probably have great ideas on how to build a schedule that’s more productive and boosts morale at the same time.
When I Work can help you build schedules that are predictable and fair, fostering employee engagement and morale, as well as increased productivity. You can use the software to create rules around rest periods and easily copy and paste shift templates to build rotating schedules that work best for your plant.
Benefits of effective manufacturing schedules
The benefits of great shift planning are reduced labor costs, increased productivity, and increased agility as a manufacturer.
When you effectively schedule your manufacturing shifts, you’ll end up with the right amount of shift coverage to meet production demand. But even more importantly, you’ll avoid burning out your employees and you’ll build a great work culture.
Employees who like their shifts, feel that shifts are being doled out fairly, or that they have some say in their work schedule, are much happier and safer. They’re willing to stay on the job instead of contributing to turnover.
The most important benefit of effective scheduling, in other words, is a solid employee base that sticks around.
Using When I Work to schedule manufacturing employees
The most obvious takeaway from all of this is that managing manufacturing schedules is highly complex. At this point, it’s too complicated for you to continue using manual methods; employee scheduling software is necessary.
When I Work is a deceptively easy manufacturing labor planning software that comes with all the features you need to create any (or a mix) of the schedule types listed above. It’s ideal for all manufacturing scheduling.
- Mobile apps mean you can manage the schedule anywhere, and employees can check the schedule anytime.
- Internal messaging and communication between managers and employees creates a cohesive team.
- Employees are empowered by allowing them to request time off or swap shifts with each other without having to get manager approval.
- Managers save time and still stay on top of things by setting up the schedule templates, shift rules, list open and available shifts, and watch for alerts on your schedule that indicate overtime issues
Sign up for a free trial today and take a look under the hood. You’ll see how every scheduling concern has an easy solution, all in one manufacturing employee scheduling software.
Manufacturing shift schedules FAQs
What is manufacturing shift scheduling?
Manufacturing shift scheduling involves assigning work times to employees to ensure full coverage that aligns with production demands. This process includes defining work shift lengths, choosing shift schedule types, and determining overtime and scheduling policies.
What are some best practices for shift scheduling in manufacturing?
Some best practices for shift scheduling in manufacturing include planning ahead to prevent last-minute changes. Be sure to comply with federal and local laws and regulations as well as internal policies. Maintain open communication with employees about the schedule, and make the schedule accessible to all employees.
What are the common types of manufacturing shift schedules?
The common types of manufacturing shift schedules include fixed shift schedules, split shift schedules, overtime shift schedules, rotating shift schedules, on-call shifts, and no-schedule shifts. The choice of schedule type depends on the unique needs of the manufacturing process and the workforce.
What are the benefits of effective scheduling in manufacturing?
Effective scheduling in manufacturing can lead to reduced labor costs, increased productivity, and increased agility as a manufacturer. It can also help to avoid employee burnout, create a better work culture, and reduce turnover by ensuring fair scheduling and allowing employees some control over their work schedules.
Why is manufacturing employee scheduling software necessary?
Managing manufacturing schedules is a complex task, especially when using manual methods.
Employee scheduling software like When I Work simplifies this task by providing features that allow for creation of different schedule types, communication with employees, shift rule setting, and overtime issue alerts. This enables a more efficient and self-sustaining scheduling process, benefiting both management and employees.